Experienced electricians quite often joke: "electrical engineering is the science of contacts." In fact, when repairing the wiring, the most common malfunction is the absence of contact. In this article, let's talk about how to properly execute.
Typically, this kind of problem occurs in the terminals, terminals, twists and other junctions of the conductors. The deterioration of contact can manifest itself not only in the "loss of light", but also in the heating of the insulation of the wires, which, in turn, can cause it to ignite.
Simple twisting of wires for their electrical connection has long been in the past - to date, to ensure a reliable contact apply special – .
Despite the fact that in the modern market there is a wide range of these elements that differ not only in price but also in some features of the design, the design of the pads is the same in all cases: brass tubing with threaded holes on both sides is installed in the cells of the casing.
Pipes can be of various diameters, depending on whether a connector is used to connect what section of wires.
The scope of the pads can be very diverse. So, for example, such a connector is simply indispensable when connecting a chandelier to short conductors that come out of the ceiling.
It is very convenient to use this connector and, if necessary, to connect the wires that are broken in the wall, as, as a rule, the damaged conductors are not long enough to connect them in any other way. True, there is one "but" here:
Of course, the reliability of the connection with a pad is definitely lower than in the case of soldered connection. However, such a connection is more convenient and requires much less time.
The undeniable advantage of its use is also the possibility connections of aluminum and copper conductors. In this case, to avoid possible oxidation, one wire is passed under each clamping screw, not allowing direct contact of the conductors with each other.
Wire connection terminal block
When selecting the connection block, first of all, consider the amount of current that will pass through the connection point, as well as the required number of mounting terminals in the comb.
As a rule, the process of connecting conductors does not cause any difficulties even for electricians-lovers.
The installation is really very simple: take the shoe with the required size of the cell, cut off the desired number of sections, insert the wires into the terminal cell and screw each of the connected conductors with screws.
Tighten the screws for fixing the conductors should be done with a moderate amount of force. Naturally, the insulation must be removed from the ends of the conductors to be connected (it is enough to remove about 5 mm of insulation), and the surface of the conductor itself must be thoroughly cleaned.
A great advantage of these pads is that, depending on the mounting conditions, each segment can be cut off. True, there is one nuance: in such a shoe, I would not recommend clamping aluminum. When tightening, the aluminum core can be driven by the screw itself.
If aluminum wires are connected, the screws must be tightened with extreme caution. The reason is that, firstly, the aluminum core can simply break down, and, secondly, it is known that aluminum has a certain fluidity under the influence of considerable pressure, which after a certain time can lead to deterioration or complete loss of contact.
And this, in turn, is fraught with overheating of the conductor and its ignition. By the way, by the standards, absolutely all compounds in which there is aluminum, it is necessary to tighten with frequency once a year.
How to connect stranded wires in a shoe
Also note that it is inadmissible to clamp multicore conductors in such a shoe. Stranded wire, like aluminum, can be driven by a clamping screw.
The fact is that in the connecting block there is everything that does not really "like" stranded wire - this is the uneven surface of the clamping screw, and the point (uneven) pressure, and rotational motion.
Of course, the installation can be quite acceptable, but it may not work out - and only a very small number of veins will remain from the conductor.
Thin wires, of which such veins are composed, are quickly deformed and damaged by the action of the clamping screw of the shoe. As a result, contact is obtained unreliable - the connection is heated and melted.
The best solution to this problem is the use of special handpieces for conductors. In household electric appliances, bushings with plastic cuffs, which for the convenience of installation are made in different colors.
The process of mounting the tips is carried out in several stages:
- 1. The end of the conductor is trimmed with the help of wire cutters (the ends of all "wires" of the core must be the same length).
- 2. The insulation is cleaned in accordance with the length of the metal sleeve of the tip.
- 3. Carefully form the parallelism of all wires (without twisting). In case the wires are twisted they are neatly straightened.
- 4. The tip is put in such a way that the bundle of wires protrudes from the sleeve approximately by 0.5-1 mm. At the same time, make sure that the cuff covers the edge of the conductor's insulation coating.
- 5. Then, with the help of special press-pliers, the tip is crimped (in the absence of this tool, crimping can be made using ordinary pliers).
- 6. After this, the conductor with the installed tip is inserted into the terminal connector and fixed with a clamping screw.
Pads with a cover for connecting the wires
Separately, it is necessary to recall the terminal blocks made of high-strength black plastic. The main advantage of such a connector is that in it the conductor clamp is carried out by the plate, and not directly by the screw.
Due to this design, it is possible to reliably connect not only aluminum, but also multi-stranded conductors. In addition, these pads differ and a higher permissible working current (you can find pads, rated for current up to 40A).
The only minus of such pads is that they are not cut and do not separate.
When wiring a wiring in an apartment or a house, there is a need for a large number of connections and branches. For switching wires, a junction box is used, and for a reliable connection of conductors, a terminal block is used. Such electrical installation equipment has various types and forms of release, which allows you to choose the most suitable option for a particular case.
Types of junction boxes
By way of installation, the junction box is of two types:
- The outer box is used in conjunction with an open mounting method electrical wires. It is installed on the wall surface;
- To mount a hidden switch box in the wall, a hollow is hollowed out into which the device is mounted. It is used with concealed wiring: this method is more popular.
The junction box has a white or black standard color. Depending on the preferences, you can choose a decorative cover of a certain color, which fits the interior.
Material of manufacture
Depending on the purpose, commutation boxes of different materials are produced. The greatest use was made of products, the body of which is made of metal and heat-resistant plastic.
- The metal housing is made of tin-plated steel or aluminum alloys by casting. Such connecting products are used in industry to connect powerful cables. For special operating conditions, the lid of the box and the connecting cuffs are fitted with gaskets. This makes it possible to make wire connections for operation under water or in case of accumulation of explosive gases;
- The plastic junction box has a body made of cast PTFE, more modern models are made of refractory polypropylene. Such products do not burn, but under the influence of high temperatures melt. It is these types of separators that are used for the installation of electrical wiring in living quarters.
Device
There are two types of device junction boxes:
- In products without terminal blocks inside for the connection of wires, twisting is applied with subsequent isolation or by means of caps;
- Some models are equipped with terminal blocks, which allow you to quickly and reliably connect and compress wires with different diameters. Another advantage of these wiring devices is the ability to connect copper with aluminum, which by twisting is prohibited.
Note! Depending on the number of planned connections, you can choose the size of the junction box. In addition, the products are square, rectangular and round.
Mounting Features
With the concealed installation of electrical wiring, all elements are laid in special grooves - shtroby. To install the junction box, the recess is made by a perforator or a special bit - a crown. The product is attached to the wall with a plaster solution or a dowel. In frame houses for the installation of boxes, special seats are prepared.
The depth of the hole is calculated so that the box body protrudes beyond the finish by 2-3 mm. This is necessary for convenient fixation of the lid.
After that, according to the previously made connection scheme, wire connections are made. An important nuance is the need to plug the end of the wire into the case of the box with a small margin (about 10 cm).
Types of terminal blocks
After the types and characteristics of the junction boxes have been studied, let's look at the main types of connection blocks used for domestic electrical wiring.
It is from the quality and reliability of the connection of wires that the safe operation of the wiring depends. Therefore, the most reliable type of connection is a screw contact with terminal blocks: they allow a good compression of the core. The terminals are suitable for single- and multicore conductors, and also allow the connection of a thick wire with a residential section having a smaller cross-section.
Depending on the type of connection and operating conditions, one of the types of terminal blocks available today is selected.
Polyethylene pads
Such products are made of white or transparent polyethylene, resistant to chemical solvents and other aggressive components. The bar consists of several pair of screw clamps, which can be cut with a knife if necessary. It should be noted that these terminals have a small internal diameter and mechanical strength. Most often they are used for connecting the wires of the lighting network, as well as connecting low-power consumers, for example, chandeliers.
Polyamide terminal blocks
This kind of shoe has better performance characteristics than the previous one. They are made of black polyamide, which does not support burning. During operation, the polyamide can be heated to 120 ° C, without changing the shape (melting). Resistant to various solvents. Such connecting devices are widely used in everyday life, since they are very convenient and practical, suitable for fast connection of any consumer to electrical wiring.
Products with spring-loaded contacts
Also convenient to use and provide reliable contact of the terminal with spring-loaded contacts. They are often used to connect electrical wires of cross-section up to 6 mm 2. A plate with a spring allows you not to worry that the stranded conductors will be damaged during crimping. Pads are made of non-flammable polyamide, available in several colors.
Carbolitic terminal blocks
To connect wires that are under heavy load, crimping blocks of carbolite are used. The base is capable of withstanding significant heating (up to 150 degrees) and mechanical impact. Contact elements are made in the form of tires from tinned brass. Crimping of conductors is carried out by means of additional plates and metal screws. In some models for additional protection and insulation of the contact strip provides a cover of a transparent impact-resistant plastic.
Important! The peculiarity of terminal blocks with screw terminals is the need for periodic revision of the state of contacts. All the screws need to be tightened about once a year, since the contact can be weakened.
Self-clamping terminals
Quickly received recognition and became widespread recently appeared relatively recently self-clamping terminals. The use of such devices does not require additional tools for connecting the wires. The peculiarity of the design of these devices is the presence in the body of a spring-loaded contact plate. To make the connection, simply brush the bare end of the wire into the terminal with a little effort. Products are produced for connecting two or more conductors, and also in the form of a terminal block. The disadvantage is the limited internal diameter of the terminal, which makes it possible to connect the conductors to 2.5 mm2.
To transfer electricity and bring it to consumers, copper and aluminum wires are used. How to properly connect them to avoid short-circuiting, oxidation and loss of contact? In this article we will discuss the principles of connecting wires and cables, whichtypes of terminal blocks for connection wiresthere are reasons to use them more conveniently and correctly than classic screw connections or twists.
Wires are thin metal conductors for electricity. They are produced in coils of 50, 100 or more meters. When creating a wiring it is necessary to break the integrity of the cables, assembling the junction boxes, connecting the wires to the shield and the consumers.
Preparing the wires for the connection in the box
Note:according to statistics, 90 percent of the problems with the electrical wiring are due to poor contacts. Electricians have a saying: "The science of electricity is the science of contacts."
All connections must be performed very responsibly, so that there are no "bottlenecks". It is not allowed to make ordinary twists or to connect wires from copper and aluminum directly, because over time the metal is oxidized, the contact surface area decreases, the resistance rises and the temperature increases under loads. In some cases, this leads to sparking and fire, short circuits and other unpleasant events, so everything must be done in a high-quality, thoughtful and thorough manner.
When assembling the electrical wiring, you need to fasten the wires to the colors, solder them, usingscrew clamps for wires or connecting terminals. The latter option is considered optimal, because it saves time, ensures high-quality connection and reliability of contacts.
Most of the connections in the last century were made by twisting - two wires were cleaned and scraped with each other, and then isolated with the help of insulating tape. Such a connection can not be called qualitative, especially if the wiring was assembled in a hurry and the ends of the wires were not propaivalis.
Today twists are practically not applied, but still they need to be able to correctly do, because it is not always possible to buy terminals for the connection.What are the terminals (terminal blocks)? These are special connections that allow splicing the ends of the wires without soldering. If the cable is not connected in a junction box, the ends are connected at different levels (so that they do not coincide vertically). The connection point is well propaivaetsya and isolates first each wire, and then - the entire cable.
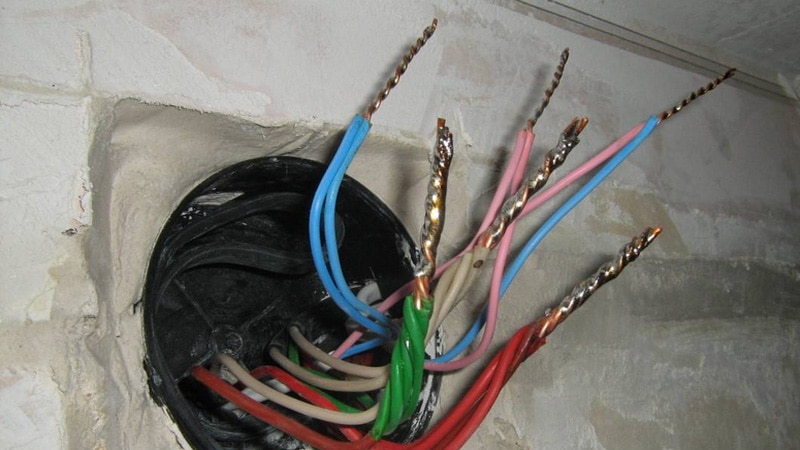
The longer the twisting, the greater the contact area of the elements (soldering increases the area 5-10 times). It is recommended to twist the wires with pliers to tighten them as tightly as possible and improve contact. Isolation of metal should be done with a reserve, overlaying the tape in several layers.
As you can see, nothing particularly complicated in this. But over time, the adhesive composition on the insulating tape dries up, it begins to unwind and possibly the appearance of short-circuiting. Therefore it is much more reasonable to usewhich are assembled from plastic, resistant to temperature changes, ultraviolet and not exposed to corrosion.
Such clamps serve for 50-70 years, without losing their qualities, their cost is quite affordable, and the process of connection is simple and does not require special tools. To connect the wires in the junction box, you can use special caps. They are like small glasses. The installation of the caps is very simple - the two wires are cleaned by 10-15 mm, twisted together, and a cap is put on top of them. It covers the exposed contacts and secures the ends, improving contact.
When buying caps, take into account the characteristics of your cable. There are caps for single-core and stranded wires, for thin and thick, with a special protective paste inside, preventing the appearance of oxidation of the metal surface. Remember, copper and aluminum wires can not be connected with each other, as they quickly oxidize.
Types of terminal blocks
There are several typesconnecting terminals for wires, so you need to understand which ones will be useful to you. First, find out which cables you need to splice: single-core and stranded, cable diameter, single, double or triple. And only after that go to the store.
The classic terminal consists of a plastic housing with a brass liner in the form of a threaded tube that keeps the cable from jumping out.The advantages of terminals include:
- Simplicity of work. In part of the devices it is enough to simply insert the metal stripped from the insulation, after which the lock works in it and the wire does not come out.
- Possibility to connect wires of different cross-section. For example, you can connect a 2.5mm2 cable with a 1.5mm2 cable.
- The ability to connect wires from different metals, because there is no direct contact between the wires.
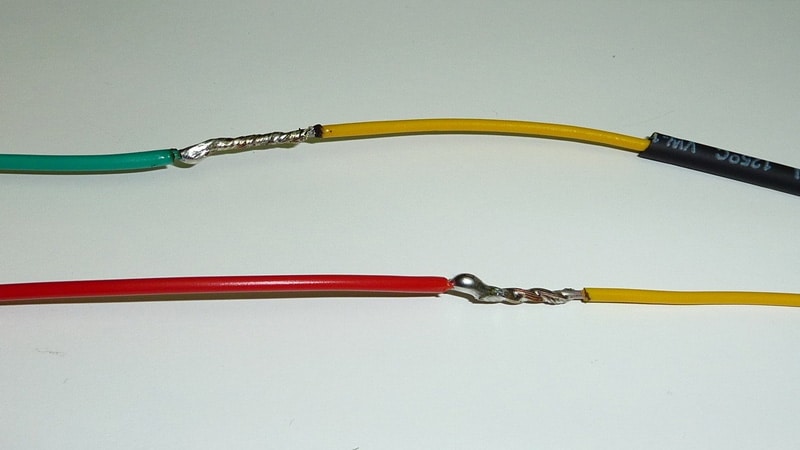
Note:terminals can withstand different currents, so if you drag a line to a powerful consumer (electric boiler, boiler, warm floor), then use powerful terminals.
Terminal clamps have proven themselves in the work - they protect the connection even better than when soldering and using electrical tape. The plastic case does not dry up and does not break, the clamp ensures a good connection between the two contacts and their integrity. The time to install the terminal is only a few seconds, while twisting, soldering and isolating one point can take up to 5 minutes.Cables are connected in terminals in three ways:
- Knife.
- Spring.
- Screw type.
Before buying, please specify which terminals are offered to you.The knife joint is good because you do not have to strip the wires - the terminal itself cuts through the insulation and pulls it to the metal. True, in order to establish it, a certain effort and experience is required. Such terminals are often called wrappers, they are used both in everyday life and in the automotive industry.
Spring devices are used both for creating wiring in a private house or apartment, and in industry. The use of spring connections is the most convenient - for this it is necessary to strip the cable for a certain length and insert the metal into the connector. The spring will securely fix the vein and will not allow it to break out even under severe load. To disassemble such a unit, it is necessary to carefully pull the lever in the terminal with an awl or a thin needle, then pull out the core. But reusespring terminals for connecting wires is not recommended, because they no longer provide a quality clamping and fixing. Get a new device - it is quite inexpensive.
Buying such connectors, think about how many live you will need to connect, because they are available in two, three, four and six contacts. When connecting, be sure not to spoil the color of the wires and phase / zero so that there is no short circuit. When connecting switches, always open the phase, and zero immediately on the lamp.
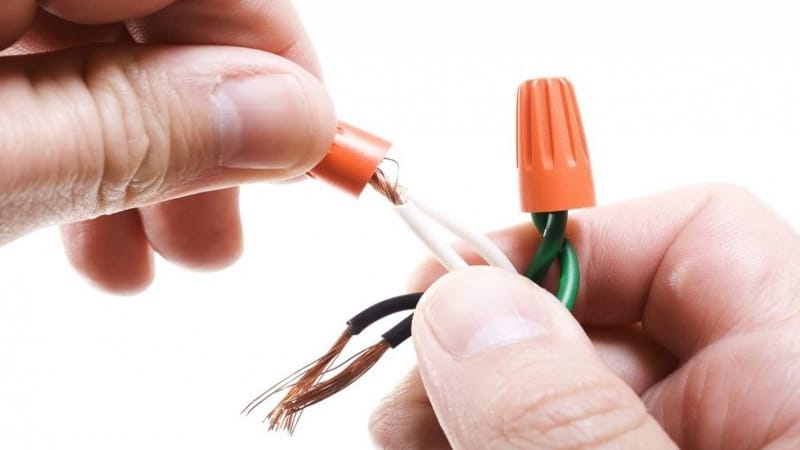
Screw connection terminal block it is also popular, although it takes more time to connect than when using a spring. The connection is as follows:
- The ends of the veins are brushed to 10 mm.
- Stranded wire twists to make its texture more solid.
- The core is inserted into the connector, from above it is attracted by the screw.
- The operation is repeated from the second side.
Note:screws tighten with a tangible effort, but do not overdo it so as not to cut the thin copper veins. The wire must not fall out or move in the terminal strip.
From the shortcomings of such a solution can be identified:
- Need to use an additional tool (cross or flat screwdriver).
- Complexity of work in a limited space (if the ends are very short and do not climb out of the junction box, then it will not be easy to install the terminal and tighten the screws).
- Installation takes several minutes. If you simply insert the end into the spring connection, then you need to tighten the screws and waste time.
- After a while, the fastening may be weakened due to the fact that the stranded wire will crumble. After a year, it is recommended to tighten the screws to ensure a better connection.
Fasteners for distribution cabinets and boxes
If you need to connect the ends of the wires in junction boxes or cabinets, then you need to use special terminals.The terminal block is the device, which consists of a body made of polycarbonate (not afraid of high temperatures and has self-extinguishing properties), in which a copper connector is mounted. In the case there are holes in which cables are inserted. The terminal blocks can be used to connect wires of various cross-sections and material, to assemble with them earthing, etc.
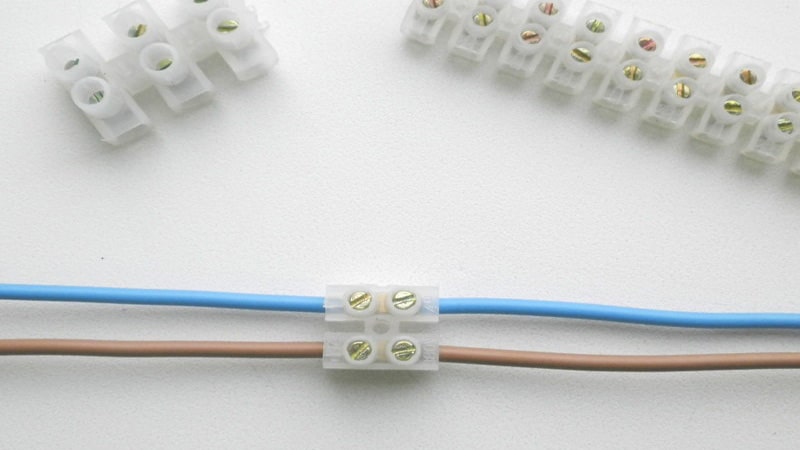
Please note that on the caseelectrical connector indicates the strength of the current that it can withstand, so be sure to think through what you will be connected to or select the slats with boundary values (for copper cable on 2.5mm2 - 25 amperes). In some pads inside there is a special paste protecting the bare ends from oxidation and heating.
Fasteners with fuses
To protect the wiring and consumers from short circuits and overloads, terminal fuses with fuses can be used. They have a special holder, into which fuses are inserted. If the load increases to critical, it burns out and de-energizes the line, protecting it from overload and reflow. Replacing the fuse does not cause any particular problems - they can be bought at any electrical store.
Lighting terminal blocks
In principle, these are conventional terminals, but designed for a small diameter of the wires, because the lighting is often routed with a cable of 1.5 mm2. The plastic housing of the terminal block withstands a temperature rise of up to 110 degrees, and the copper fastening tube allows fast connection of the wires without wasting time on soldering or twisting of the screws. Since the lighting network rarely has a current strength above 16 amperes, the terminals are made in small sizes, for 2-4 connections. If necessary, they can be combined with each other if more wiring is required. Often in copper contacts, there is a paste to protect the ends from oxidation and the removal of excess heat.
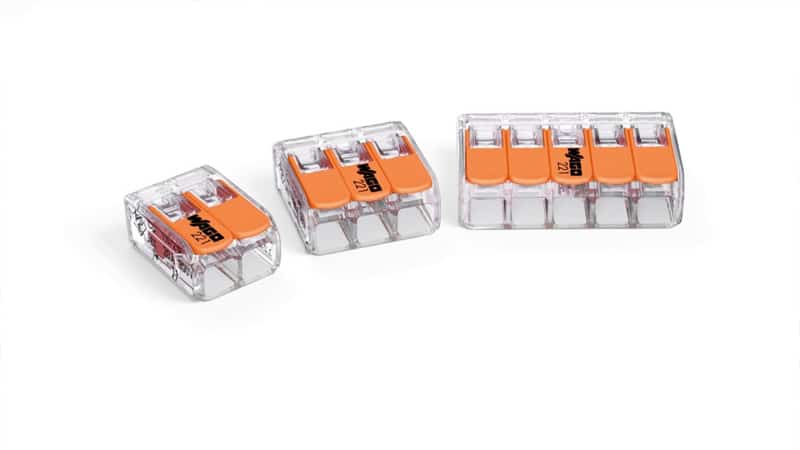
Devices for connecting chandeliers and lighting fixtures
When connecting fixtures, fans, chandeliers, floor lamps or zone lighting, we also recommend usingconnecting blocks for wires. This helps speed up the connection process and make it easier. For chandeliers wide pads for 4-6 joints are used, for spot lights - 2 contacts. Since there is no large current in these nodes, the terminals are also made small. They are able to effectively remove heat through the thermal paste and protect the ends of the veins from oxidation. The principle of connection is the same as in the above methods - screws, springs or knives.
How to properly connect copper and aluminum
Copper and aluminum can not be joined directly to each other, since they oxidize very quickly. For this purpose it is well suitedIt turns out that the copper end is attached to a brass tube, and brass to aluminum. In this case, there is no oxidation of the contacts, when the wires are heated they do not disconnect and do not diverge.
Also practice the splicing of two materials through washers and screws. The washer is put on the screw, copper wire wrap around the screw, put another washer on top, then wrap the aluminum, again the washer and the whole structure is compressed with a nut. It turns out that copper and aluminum do not touch each other, but at the same time they have reliable contact through the washer and screw. More complex circuits with two nuts are allowed (copper is clamped separately, aluminum is separately), but, most importantly, the two materials do not touch each other, since the contact between them will quickly begin to "float" and disappear. It is best to useclamping terminal - it helps quickly and securely splice two wires from any materials.
The safety and durability depend on how reliable and reliable the electrical connection will be. A good contact between the wires gives a stable and even voltage without shorts and jumps. But if sometimes you can do with the usual twisting, in most cases this approach is unacceptable, and you need to use terminal blocks to connect the wires. "Why?" - you ask. Let's figure it out.
Is the terminal better than twisted?
Many electricians, among whom there are very qualified and experienced specialists, say that it is better than any comb - the usual twist. This statement is true, but only in part. The fact is that a lot depends on what equipment we are dealing with, what material the connected wires are made of, and from other factors. This at first glance may seem like a trifle, but in fact everything is somewhat different.
Let us mention one interesting fact. The rules for conducting electrical work say that twisting in any connections is prohibited. For this simple reason, any tragedy that will occur because you used a forbidden connection will happen through your fault. In addition, only 4 types of connections are allowed, we will talk about some of them in this article.
What is a terminal strip?
A terminal block is a special device, which is a screw terminal or shoe. It is used to securely connect wires. There is a huge number of standard sizes of modern combs. But it is worth noting that the terminal blocks for connecting the wires are used to easily fix the cable without damaging it.
There are several methods of fixing the wire, the most popular is fastening under the screw head. Forced pulling through the screws of the screw connection is also used. As a result, you can get a very reliable contact and do not cause mechanical damage to the wire.
In some cases, terminal blocks for connecting wires have special tips. They insert a cable, which then joins electrical cabinet or any other equipment. Such combs are called pass-through.
Screw terminal and its description
The area of application of screw combs can be talked for infinitely long. In fact, these are the most popular terminal blocks, the design of which is reliable and at the same time simple. This kind of devices are used not only for wiring, but also in sockets. They are also used as a clamp for connecting groups of fixtures and much more.
As for the material of manufacture, screw terminals for connecting wires are often made of polypropylene and polycarbonate, but sometimes they are made of polyamide and polyethylene. You should understand that this kind of device is not suitable for working with aluminum wires. This is due to the exceptional fragility of the latter, so when fastening you can damage them. But for copper and other wires, this is exactly what you need. Often the screw terminal block is made grounding. In this case, as a designation, it has a green screw, as well as special dents for effective wire gripping.
Clamp connection
The screw terminals, which we have examined, are one of three kinds of connecting devices for wires. According to the PUE, it is advisable to use them also. They are used to fix and connect wires with a cross section of no more than 2.5 mm at a current of 24 A. Such a comb withstands a load of the order of 5 kW. If the equipment is more energy intensive and powerful, then another method will be required.
Interestingly, it is possible to connect this type of terminals to 8 wires, for which there is an appropriate number of sockets. Such a decision contributed to the fact that it was possible to significantly accelerate wiring electrical wiring.
The above method has one drawback. It concerns the occupied space in the junction box (and that only in comparison with twisting). The level of safety and reliability of the contact in this case is much higher, if not exceed the permissible load. Otherwise, the connection of this type of terminal can be inefficient and even dangerous.
Insulated terminal blocks for electrical wiring
The connecting insulating clips (PPE) are similar in appearance to the plastic cap. They are made of non-flammable polymer, which eliminates spontaneous combustion as a result of temperature increase. You can say that their main purpose is to protect them from fire. Nevertheless, PPEs have a positive effect on the quality of the connection by providing a reliable mechanical contact. To do this, they must be twisted into twisting in the direction of twisting the wires in the cable. As a result, the spring inside the housing compresses the wires of the wire, thereby improving contact. Processing twisting with a special paste will avoid oxidation.
If terminal blocks are used for this type of wiring, it is possible to reliably connect wires of different diameters. You can also create a contact between the copper and aluminum wire. In addition, the spring has a permanent effect on the fixed wires, so there is no need for periodic inspection, as in the case of screw connections.
We should note several significant advantages of PPE, which consist in obtaining a fast and reliable connection, which can be done even by a beginner.
In short about power terminals
It can be said that the power terminal block has a more complex and cumbersome design than the above options. This is due to the fact that such a device allows you to connect wires of large cross-section and power (usually we are talking about a wire from 35 to 300 mm square). They are installed on a special mounting plate or din-rail, so they are often sold in several versions at once. The contact is covered with a tin alloy. The clamp has tapered washers, which completely prevents the contact from loosening. Sometimes the power terminal block allows you to install a couple of additional jumpers to the adjacent terminals, which can be very convenient.
Barrier and universal terminal blocks
A distinctive feature of the barrier terminals is that they have in their design the small ones are separated by an insulating layer. This will be a good distribution board, since it completely eliminates the contact of neighboring wires. High quality is also due to the fact that each wall has a pair of screws. They are needed for reliable attachment of contacts.
In particular, barrier terminals are installed, because they are very convenient and reliable. Universal combs are a distribution block with a metal tube, each of which is equipped with a pair of screws for fixing the wires. This is very convenient when you need to branch the wiring.
Conclusion
Now you know what terminal blocks are for connecting wires and what kinds of wires they are. It is worthwhile to understand that such devices allow making the connection not only durable, but, more importantly, reliable. Currently, there is a huge number of terminal blocks available for sale. Some are suitable for wires of small cross-section, others for large ones. There is a screw terminal block, screwless or bolted. They all have their strengths and weaknesses. For this simple reason, the choice must be justified, only then one can hope for a positive result.
During the wiring process, each master necessarily encounters such an occupation as connecting the sections with a wire between them. The most common wiring fault is short circuit. Also, a very frequent unpleasant phenomenon is the breaking of a chain, most often it happens at the place of connecting the wires. These compounds are produced in and mounted in the plane of the wall or on its surface. Often inside these boxes are connections of wires that lead to the automatic switchboard, as well as the wires that go to the outlets, and the lights. In parallel, they can be laid another wire that connects the boxes to each other. Connections of this kind are always strictly identical to the design schemes.
Below you will find the most common types of connections:
- With the help of twisting and further.
- With the help of "nuts".
- Using the terminal blocks.
- With the help of spring terminals WAGO.
- By means of connection of zeroovikov connecting buses.
- With bolted connections.
- Through .
Terminal blocks
The use of this switching option is the most in demand because of the minimum labor costs for installation and compliance with all standards. A separate advantage is the ability to connect wires of different cross-sections and material. Nowadays the market of electrical materials is full of various goods, but these terminals are undoubtedly the leaders in sales.
Types of wire terminal connections
Terminal clamps allow to exclude contact of wires from various materials in a connection of wires. To date, the leaders in the field of electrical connections there are 3 types of terminal blocks:
- Spring type.
- Screw type.
- Knife type.
Pads are mainly made of brass. They consist of assemblies of 2 or more terminals. Individual varieties are filled with a specialized gel to protect against corrosion from outside. They differ among themselves in terms of: the diameter of the connecting wires, the voltage and the amperage.
At present, this type of wire connection, like conventional twisting, has come to the back burner. To ensure reliable contact at the junction of the electrical wiring, use special terminal blocks, which are called terminal blocks. In the modern market of our country there is a huge number of such pads. They differ among themselves: a price tag, a design and some performing features.
The construction of the shoes is identical. It consists of the body itself, inside which there are special cells, and inside the cells there are already brass tubes with several holes for threading.
The tubes themselves are of different cross-section, they are selected according to the diameter, corresponding to the diameter of the wires themselves.
Apply terminal blocks in a wide variety of locations. An example is the way to connect an ordinary chandelier in an apartment, connect it to short conductors sticking out of a hole in the ceiling.
This method is often used to connect wires that are broken and located in a wall. Often, such conductors do not have enough length for subsequent connection in another way.
Advice from the master: "The pads should be located directly in the junction box. Their location inside the plaster is strictly prohibited! "
Although this connection is inferior to the connection in its reliability, but in the end it is more convenient and requires minimal time costs.
The main advantage of terminal blocks is the fact that they can connect aluminum and copper conductors. To exclude the oxidation process, in this case only one wire is passed through the clamping screws, the contact between the strands is completely eliminated.
WAGO terminals. Design features and differences from other terminals.
The company WAGO (WAGO Kontakttechnik GmbH & Co. KG) was founded in 1951 in Germany. It started its production with the development and introduction of spring terminals, which has greatly succeeded. Until now, the company is engaged in the production of this electrical equipment and finds only positive feedback in the electronics and electrical engineering market.
1973 marked the beginning of the release of the first small-sized terminals to. Further, this production was patented, and production began to grow. To date, VAGO is the world leader in the production of terminals on springs and other connectors required for the installation of electrical wiring.
The main advantages of spring terminals are:
- High level of vibration resistance of the obtained compound.
- The very point of contact is securely fixed, thanks to the spring pressure. This feature makes it possible to avoid plastic deformation of the metal.
The wiring terminals for WAGO wires have passed all kinds of international electrical wiring certifications. They can be used when reconnecting the wires. Also, the terminals are equipped with technological holes for connecting the probe to the thin carrier bus. The products do not require the use of a special tool.
The terminal group includes both springs and finely bearing busbars. These tires are made by tinning copper. This fact provides protection from corrosion and increases the contact area of the cores.
Springs are of flat shape, they are made of austenitic steel. Due to this, they have increased elasticity.
The housing for these terminals is electrically insulating. It is made from modified polyamide and polycarbonate. These substances have high resistance to ignition, self-extinguishing, they are resistant to fuels and lubricants and other external influences.
Wire connection using terminal blocks
The choice of the pad for connecting the wires is a responsible action. It is necessary to pay attention to the current strength, which will then run through this product. It is also necessary to purchase the required number of mounting terminals.
The process itself is not a complicated procedure, even the amateurs will be able to conduct it, having the initial necessary knowledge and skills.
The block is selected according to the size of the cell, all the extra sections are cut off. Most often, terminal blocks are made.
Before removing the conductors from the connecting ends, the wires are inserted into the terminal cells and all the conductors are clamped with screws. The surface of the core must be cleaned. A small force is allowed when tightening the screws.
In the case of joining aluminum conductors, the screws are tightened very carefully, without any special pressure. This is done to eliminate the breakage of the wire and the deterioration of the contact in the future, since this metal has a high fluidity with strong heating.
Advice from a specialist: "Units and assemblies in which aluminum compounds are present must be tightened every year."
Conclusion
The presence of a good and reliable contact depends on the choice of quality supplies and the proper production of the operation itself. It is worth paying attention to the stability of the entire electrical circuit, connected equipment and other systems. Only qualitatively done work on connecting electrical wires and knowledge of the necessary standards, can eliminate various troubles with electricity and the operation of electrical appliances in the future.